
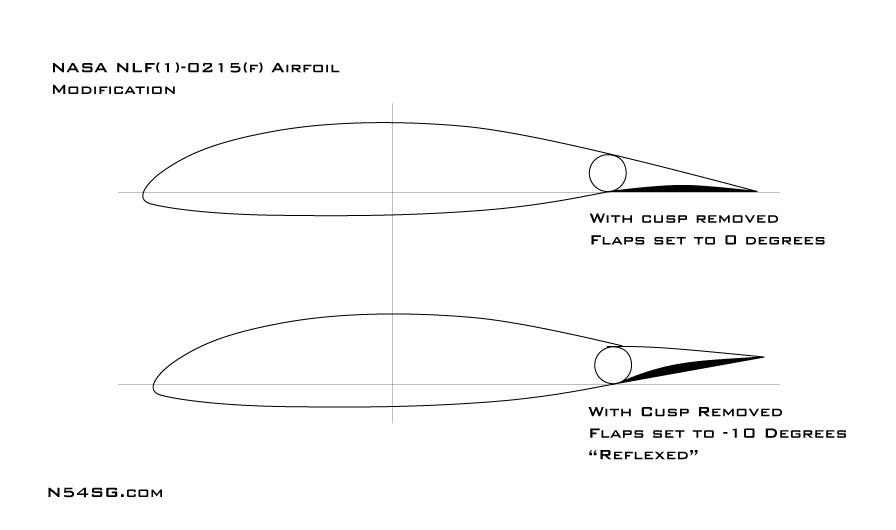
As an example of the flexibility of the surface generator, Fig. Thus, it is possible to obtain different blade surfaces by using the same constructive parameters (that is, basically the planform) and mounting different airfoils (which may differ in shape and radial position).
Airfoil camber generator#
The blade surface generator first reads the blade model (with airfoil shapes and radial distribution) and constructive parameters, and then depending on the actual radial position, each airfoil geometry, is scaled according to the given chord, rotated according to the specified built-in twist, etc., for all of the constructive parameters. This resultant force is assumed to act through a definite point located in the airfoil so that the behavior will be the same as if all the individual components were acting simultaneously.įundamentally, using the information contained therein, the blade geometry is constructed into two separate input files: the first one with blade constructive parameters (the planform data including twist) and the other with the blade model ( airfoil shapes and their radial distribution). This resultant force can be resolved into a lift component L at right angles to the undisturbed air stream, and a drag component D, moving the airfoil in the direction of flow motion. The vectorial sum of these pressures will produce some resultant force acting on the blade. Measurement of the pressure at various points on the surface of the airfoil will reveal a pressure distribution as shown in Figure 7-7 (c). On the underside of the airfoil, the action separates the streamlines, resulting in a static pressure increase. Examination of the streamlines about the body shows that over the top of the airfoil, the lines approach each other, indicating an increase of velocity and a reduction in static pressure. The presence of the airfoil has changed the local pressure distribution and, by the Bernoulli equation, the local velocities. The local deflection of the air stream can, by Newton's laws, be created only if the blade exerts a force on the air thus, the reaction of the air must produce an equal and opposite force on the airfoil. The upstream disturbance is minor compared to the downstream disturbance. The air undergoes a local deflection, though at some distance ahead of and behind the body the flow is still parallel and uniform. If the airfoil is set at the angle of attack to the air stream (as in Figure 7-7 (b)), a greater disturbance is created by its presence, and the streamline pattern will change. Flow around an airfoil at various angles of attack.
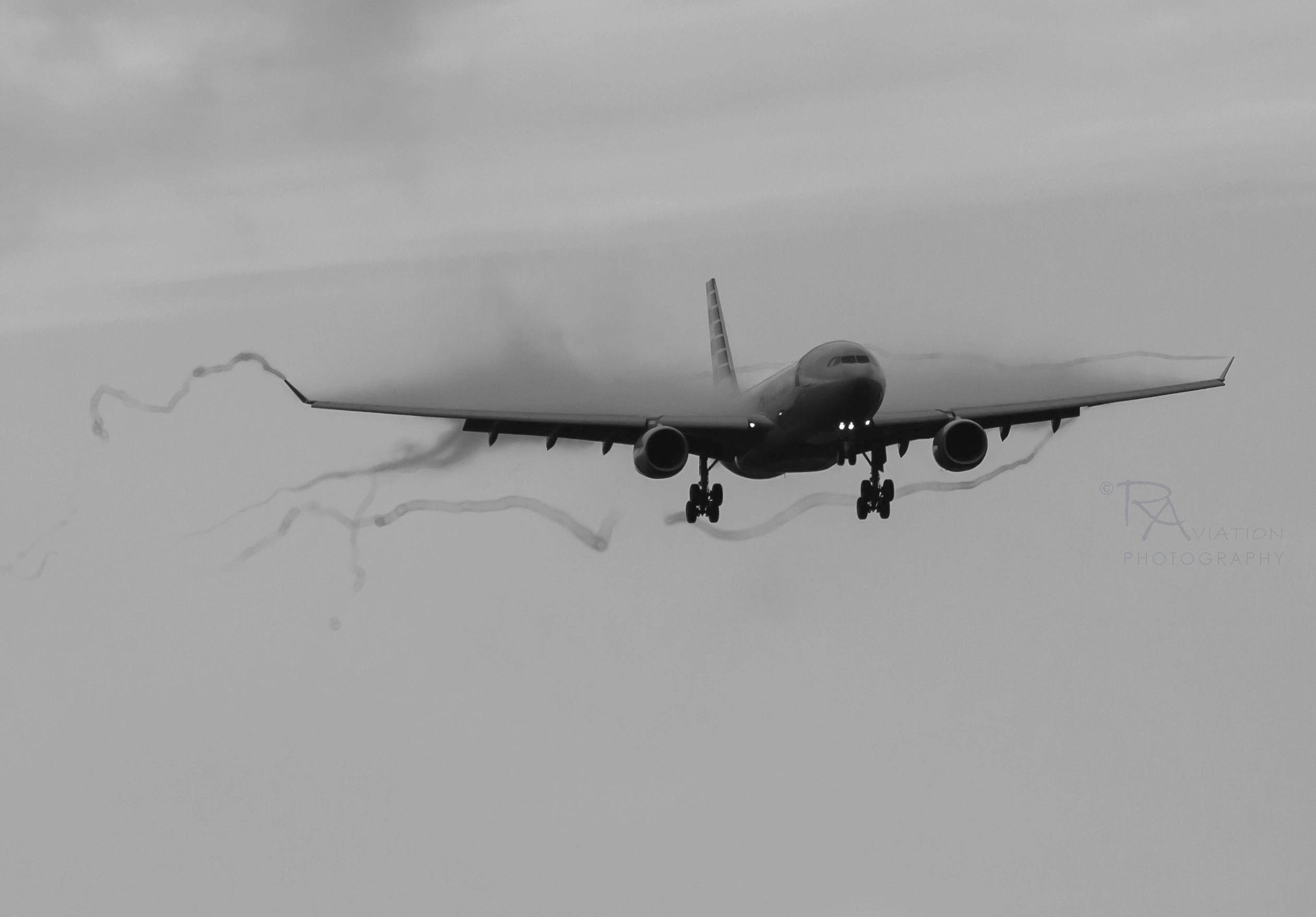
In addition to the wave drag, additional drags due to viscous and finite-span effects, considered in the preceding chapter, act on a real wing.įigure 7-7. The magnitude of the supersonic wave drag is independent of the value of the viscosity, although the energy spent in overcoming this drag is finally dissipated through viscous effects within the shock waves. The supersonic wave drag is analogous to the gravity wave drag experienced by a ship moving at a speed greater than the velocity of surface gravity waves, in which a system of bow waves is carried with the ship. The d’Alembert paradox therefore does not apply in a supersonic flow. The drag in (15.70) is the wave drag experienced by a body in a supersonic stream, and exists even in an inviscid flow. The flow in Figure 15.27 does leave the trailing edge smoothly.

However, in a supersonic flow it is not necessary to invoke the Kutta condition (discussed in the preceding chapter) to determine the magnitude of the circulation. Note that the flow in Figure 15.27 does have a circulation because the velocities at the upper and lower surfaces are parallel but have different magnitudes.
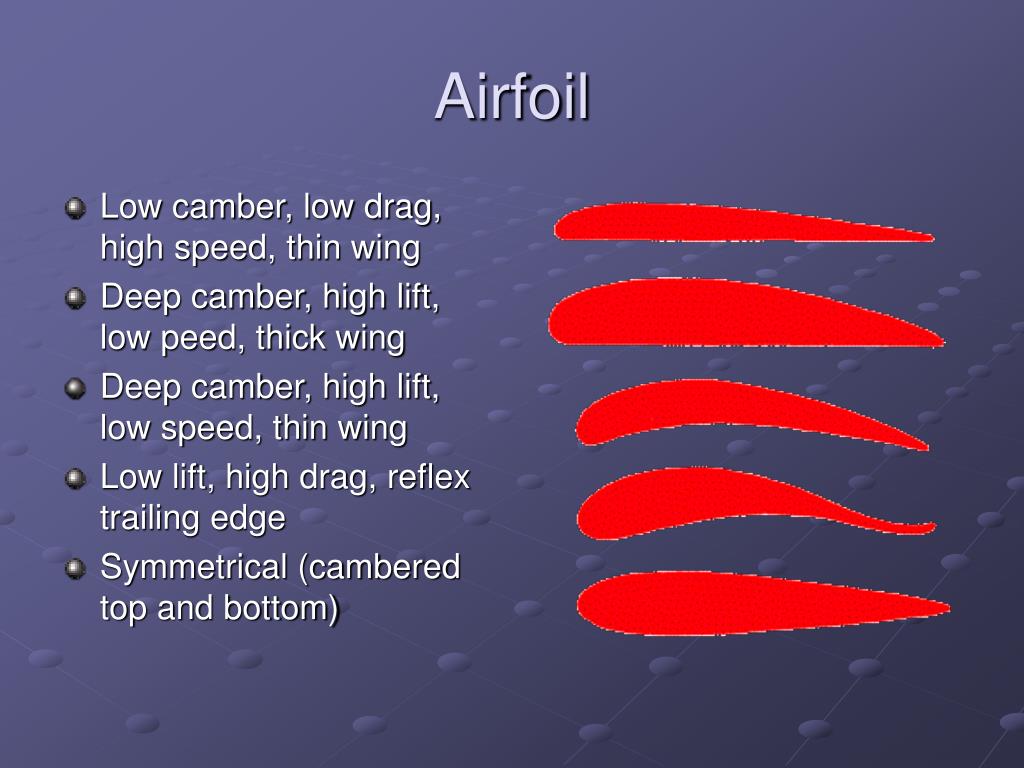
The expression for the lift coefficient should be compared to the incompressible expression C L = 2 πα derived in the preceding chapter. These expressions do not hold at transonic speeds M ∞ → 1, when the process of linearization used here breaks down. It is, however, not important to distinguish between shock and expansion waves in Figure 15.27, because the linearized theory treats them the same way, except for the sign of the pressure changes they produce. The streamlines above the plate turn through an angle α by expanding through an expansion fan, downstream of which they become parallel to the plate with a pressure p 2 p ∞. The streamlines ahead of these waves are straight. At the leading edge there is a weak expansion fan above the top surface and a weak oblique shock below the bottom surface. To see how the lift and drag of a thin body in a supersonic stream can be estimated, consider a flat plate inclined at a small angle α to a horizontal stream ( Figure 15.27).
